ETG officially supports EtherCAT G
December 2019
Fieldbus & Industrial Networking
The Technical Committee of the EtherCAT Technology Group (ETG) has accepted EtherCAT G as an addition to the EtherCAT standard. Moving forward, EtherCAT G, which extends EtherCAT technology to 1 and 10 Gb/s, respectively, will be supported and promoted by the ETG.
EtherCAT G was introduced by Beckhoff Automation in 2018 as an extension of the EtherCAT standard. Beckhoff recently presented the gigabit technology addition to the ETG, and after thorough review, the organisation’s Technical Committee accepted it. Dr Guido Beckmann, chairman of the ETG Technical Committee, explains: “EtherCAT is already the fastest industrial Ethernet fieldbus, and will remain so due to its special functional principle. With EtherCAT G, particularly data-hungry applications, such as machine vision and high-end measurement technology, can now also be integrated, which extends the range of applications.”
The well-known 100 Mb/s EtherCAT technology remains the proven solution for the majority of applications. However, EtherCAT G offers additional user advantages, especially in applications where particularly large amounts of process data must be transported per device. This can include, for example machine vision, high-end measurement technology or complex motion applications that go beyond the scope of classic drive control. Existing devices designed for 100 Mb/s can be seamlessly integrated into an EtherCAT G system, and EtherCAT G devices in a 100 Mb/s EtherCAT system behave like classic EtherCAT devices.
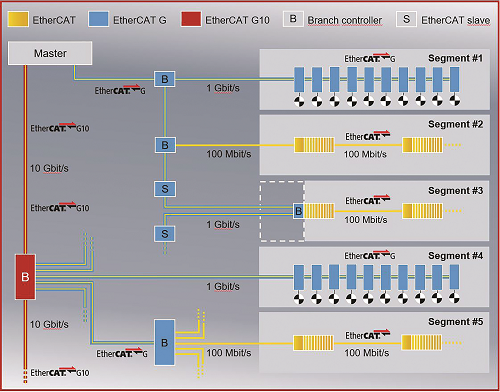
The central element of EtherCAT G is the use of EtherCAT Branch Controllers, which essentially fulfil two functions: On the one hand, they act as a node for the integration of segments from 100 Mb/s devices; while on the other, they enable parallel processing of the connected EtherCAT segments. This significantly reduces the propagation delay in the system, which increases system performance.
The integration of EtherCAT G is simple as the extension is fully compatible with the IEEE 802.3 Ethernet standard, and no software adaptions in controllers are required standard modes. “The advantages of EtherCAT are well known and include processing on the fly, comprehensive diagnostics, simple configuration and integrated synchronisation,” concludes Beckmann. “These attributes are of course fully retained when EtherCAT G is used.”
Further reading:
Beckhoff’s XPlanar boosts productivity in medical device assembly
Beckhoff Automation
Fieldbus & Industrial Networking
The intelligent transport system, XPlanar from Beckhoff provided the basis for an innovative system concept allowing the specialists at Automation NTH to reduce the space requirement of an assembly machine for medical diagnostic devices by a factor of 10.
Read more...
Comprehensive solutions for the food and beverage sector
RS South Africa
Fieldbus & Industrial Networking
RS South Africa is reinforcing its commitment to the country’s dynamic food and beverage sector, backed by a comprehensive portfolio of over 800 000 products, extensive technical expertise and end-to-end service capabilities.
Read more...
Case History 198: Cascade control overcomes valve problems
Michael Brown Control Engineering
Fieldbus & Industrial Networking
A large petrochemical refinery asked me to perform an audit on several critical base layer control loops. This article deals with a problem found on a valve controlling the flow of fuel to a heat exchanger.
Read more...
Improved networking technology for fire and gas detection
Omniflex Remote Monitoring Specialists
Fieldbus & Industrial Networking
Critical alarm and event management technology supplier, Omniflex has worked with the South African Nuclear Energy Corporation to upgrade equipment providing digital and analogue signals for its safety critical fire and gas alarm systems.
Read more...
PC-based control for fertiliser
Beckhoff Automation
Editor's Choice Fieldbus & Industrial Networking
On a farm in the USA, valuable ammonia is extracted from slurry and processed into ammonium sulphate. NSI Byosis has transformed this complex process into a flexible modular system. This modular approach requires an automation solution with flexible scalability in both hardware and software, which this Dutch company has found in PC-based control from Beckhoff.
Read more...
Loop signature 28: Things to consider when tuning.
Michael Brown Control Engineering
Editor's Choice Fieldbus & Industrial Networking
I was giving a course at a remote mine in the middle of the Namibian desert. We were discussing tuning responses, and as I always do on my courses, I mentioned that in my opinion ¼ amplitude damped tuning is not desirable, and is in fact not good.
Read more...
How industrial network design impacts ESG commitments
Omniflex Remote Monitoring Specialists
Fieldbus & Industrial Networking
In safety-critical industries like nuclear, petrochemical and oil and gas, installing a new industrial cable network is an extremely complicated task. Gary Bradshaw, a director of industrial network specialist, Omniflex explains why this is often unnecessary as plants are likely to have existing cabling capable of being used to create new industrial networks.
Read more...
Minelert industrial solutions
Fieldbus & Industrial Networking
Profitek provides cutting-edge industrial networking, automation and IoT solutions for harsh environments.
Read more...
The ultimate industrial LoRaWAN gateway
Fieldbus & Industrial Networking
The GW-101-LORA-4AO is the ultimate industrial LoRaWAN gateway, combining advanced IoT connectivity with expandable I/O.
Read more...
Industrial Power-over-Ethernet DC injector
Fieldbus & Industrial Networking
The ML-NET-INJECT series sets the standard for industrial PoE, featuring IP68-rated RJ45 connectors and military-grade components for extreme reliability.
Read more...